Expansion joints are essential for maintaining a commercial building’s structural integrity by allowing movement caused by temperature shifts and building settling. The joints are separations between the building sections, such as concrete slabs in a parking garage or between walls and floors. Without these joints, the concrete or walls could crack as the building expands and contracts. These joints are a critical area for waterproofing that often gets overlooked. To protect the commercial building from water intrusion and structural damage, it’s essential to waterproof expansion joints.
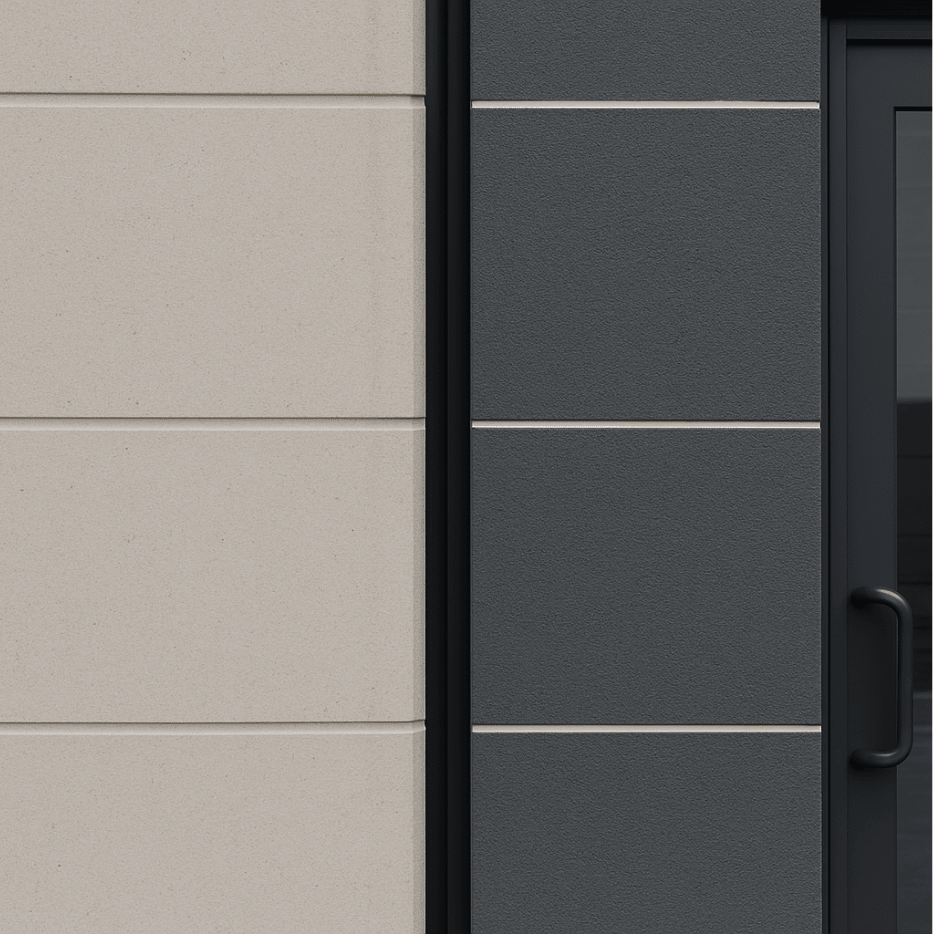
Benefits of Waterproofing Expansion Joints
Structural Integrity – Without waterproofing, water can seep into the joints and surrounding materials. This can lead to corrosion, warped and damaged materials, and overall weaken the building. If this leak isn’t repaired, it can lead to structural damage.
Reduce Repair Costs – When it comes to waterproofing, it’s important to be proactive. Waterproofing the joints will prevent damage from starting. This will greatly reduce repair and maintenance costs in the long term.
Extends the Life of the Building – The sealant used to waterproof expansion joints adds an extra layer of protection to the area. This seals out moisture and reduces wear and tear, extending the life of your building and keeping it looking better for longer.
Energy Efficiency – When you waterproof expansion joints, it not only protects against water intrusion but also air loss. If there are holes or gaps in the joints, the air from the interior of the building can leak out, causing your HVAC system to work hard to cool the building. This can cause a huge increase in energy costs. Waterproofing the joints prevents this and ensures your building stays energy efficient.
How We Waterproof Expansion Joints
Expansion joints are often waterproofed with polyurethane or elastomeric sealants. The sealant is applied to the area and then cured to create a seamless, flexible waterproof membrane. Expansion joints can also be waterproofed with pre-formed joint systems. These are often constructed from EPDM or rubber. The system is designed to expand and contract as the joint does. This method is often used in parking garages or other horizontal applications.
Expansion Joint Maintenance
Expansion joints should be checked by a professional for damage at least twice a year and after any major weather event, if external. If there is any cracking, joint separation, or bubbling in the sealant, repairs should be made. Expansion joint waterproofing systems usually last 10 to 15 years with proper maintenance.
Expansion joints are designed to allow for structural movement, but without proper waterproofing, they can become a point of water intrusion. This makes it critical to waterproof expansion joints with high-performing, quality sealants and systems.
Contact us today through our website here or call 713-699-4777 to talk to one of our waterproofing experts about your building’s waterproofing needs.
Check out our blog here to learn more about the services we offer.