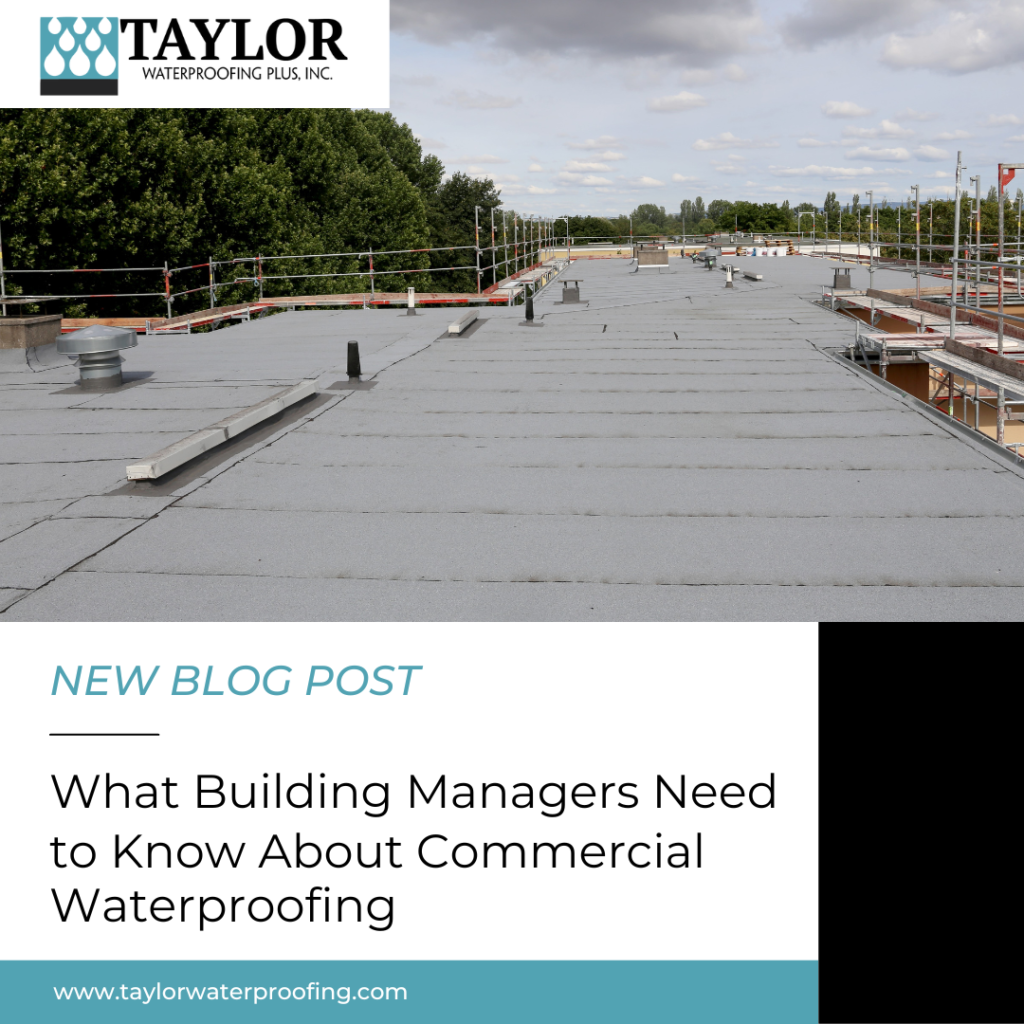
What Building Managers Need to Know about Commercial Waterproofing
If you own or manage a commercial building, your schedule is probably packed with a long to-do list. One thing that sometimes gets overlooked is waterproofing and inspections. This is a mistake when trying to protect and maintain the building. Being proactive with waterproofing will save you money in the long run on costly repairs. Here are some important things that building managers need to know about commercial waterproofing.
Why is Commercial Waterproofing Important?
Water damage not only causes cosmetic damage but can be detrimental to the health of the building occupants and cause structural damage to your building. If left untreated, water damage can cause mold and mildew growth in the building, causing health concerns. Waterproofing before these damages occur can ensure the longevity of your building and save you on repairs.
What Causes Leaks or Other Water Damage?
There are many places where water damage and leaks can happen. Water can leak out of pipes, from the roof, and even infiltrate the walls and interior of the building through concrete. A professional will assess the damage and determine the cause.
Using the Right Sealant
There are many different types of sealants and coatings that are made from different materials, such as silicone, acrylic, and polyurethane. Some sealants go on clear or glossy, while some act more as paint. Others have a thicker consistency for filling in gaps and joints. The one you decide on will be based on your waterproofing goals, the material you’re planning on waterproofing, and the aesthetic you are trying to achieve. Our team can give you all your options and help you pick what material is right for your project and building.
Concrete Needs to be Waterproofed
Whether it’s the concrete of the foundation, in the parking garage, or the floors inside of your building, concrete needs to be waterproofed. Water can seep into the pores of the concrete and cause the metal reinforcement to corrode or cause water damage to the surrounding areas. There are many options for waterproofing concrete and depends on where the concrete is located.
Inspections are Key
When it comes to waterproofing, inspections will help you stay proactive. A professional inspection will pinpoint where there is damage or where there could potentially be damage in the future and assess if any materials or sealants need to be replaced. This will prevent water intrusion and stop any leaks from getting worse.
Our team can help building managers and owners with any of the above and more. Your building will be in good hands with our trained and experienced waterproofing professionals. Contact us here to learn more about waterproofing your building.
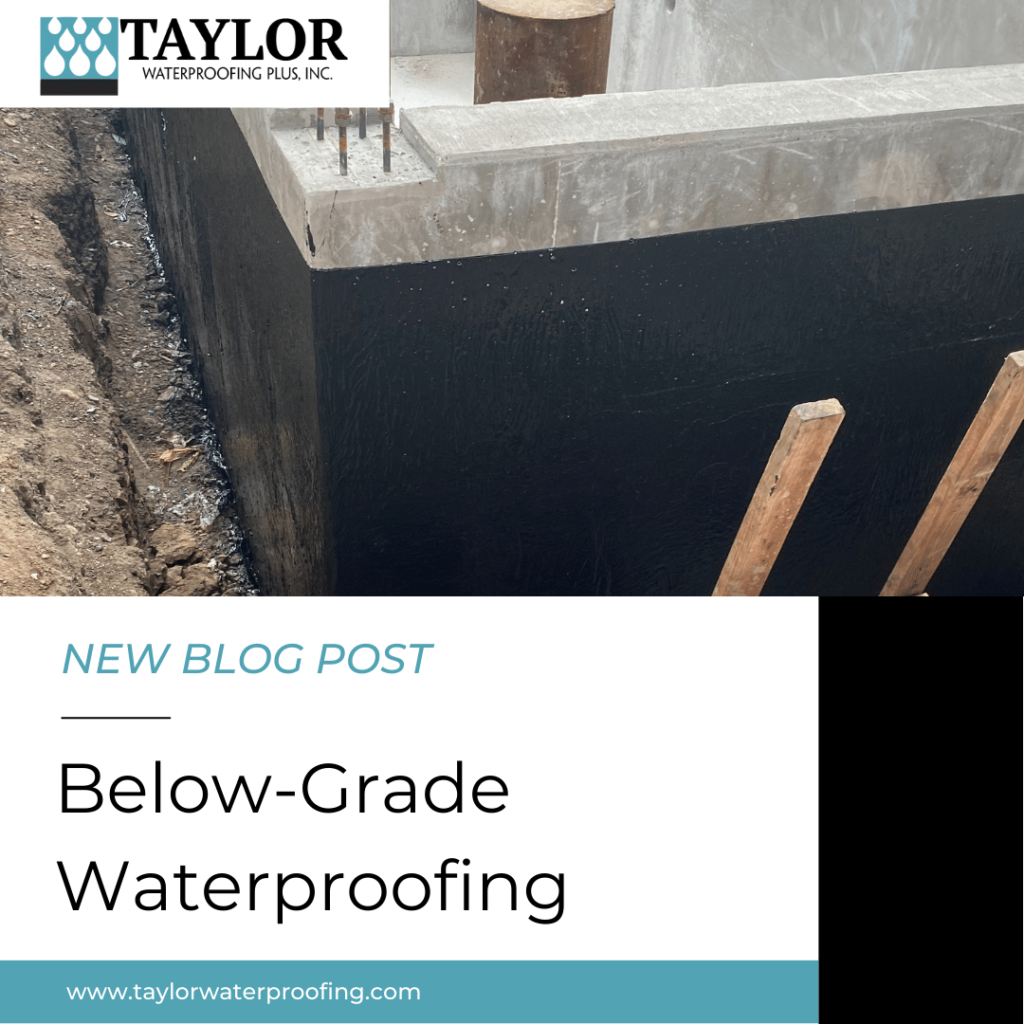
Below-Grade Waterproofing
When you are constructing a building or unground structure, such as an underground parking garage or basement, you’ll need below-grade waterproofing to make sure it keeps its structural integrity. These areas are subject to flooding and waterproofing is a way to prevent damage and increase the life of the structure. There are a few ways to install this waterproofing system, but the process refers to applying a waterproof coating or other material to the walls of the foundation, usually during the construction stages.
Because buildings’ foundations are constructed of concrete, it is porous and can crack over time. One health hazard to consider is mold and mildew growth due to water damage. Below-grade waterproofing creates a barrier between your building’s foundation and the earth. Along with below-grade waterproofing, making sure the building has proper drainage is also a huge aspect of mitigating these types of issues.
Below-Grade Waterproofing Types
Positive-Side Waterproofing – This application is done on the outside of the foundation where it will touch soil. This can consist of fluid-applied seamless membranes, sheet systems, or a combination of the two.
Negative-Side Waterproofing – This is applied to the interior of the building. It stops water and other materials from entering the building but not from penetrating the foundation. Because of this, it is usually done in conjunction with positive-side waterproofing or when the positive-side can not be done.
Overall, below-grade waterproofing protects your building by ensuring there is a barrier between the foundation and the outside elements. Without waterproofing, you could deal with structural issues, flooding, water damage, and toxic materials. When done correctly, below-grade waterproofing greatly reduces the risk of damage and protects your building and investment. To talk to one of our team members about the best waterproofing options for your project, contact us today!

Davit Testing and Why it’s Important
What is a Davit?
If you are planning on having your building’s windows washed or waterproofed, the first thing you want to consider is safety. Roof davits, also referred to as tie-back anchors or tie-downs, allow contractors or trained employees to access the facade of the building. By using a davit, you can suspend a platform down the side of the building so the individuals performing the service can have a steady and safe working platform for maintenance, cleaning, and repair services. These anchors are required for any building with 4 or more stories and 3 or more stories if ground equipment can not easily reach areas that need to be repaired or maintained.
Davit Specifications & Testing
Davit testing and inspections are an important part of your building’s safety. OSHA has several standards to regulate davits to ensure safety. Davits must be ASTM A36 steel construction and fully galvanized finish to ASTM A123 standards. After the davit is installed on your roof, it must be tested and inspected.
A davit system must be recertified every ten years. Recertification is required every five years if adhesive, epoxy, or chemically bonded anchorages are used. When testing the equipment to OSHA requirements and certification, a load test will be done to verify the strength of the davit. These anchors need to withstand an ultimate load of 5,000 lbs in any direction. While it is required that the davit be recertified every ten years, a visual inspection will need to be performed once a year.
Why is Davit Testing Important?
There are many reasons to have davit testing performed. It ensures that your building is up to code and help prevents falls. It is a vital part of ensuring a safe work environment. This also keeps you in compliance with OHSA and other government agencies regulations.
Our team can help you make sure buildings and davits are up to code and safe. Our trained professionals ensure structural integrity and compliance through testing and visual inspections. Contact us today to learn more about davit testing or schedule a service.